317L / 317 Stainless Steel Plate – High-Performance Corrosion-Resistant Alloy
Sandmeyer Steel Company has the heaviest and largest inventory of Alloy 317L stainless steel plate in thicknesses from 3/16″ through 4″.
Available thicknesses for 317 / 317L:
4.8mm | 6.3mm | 7.9mm | 9.5mm | 12.7mm | 15.9mm | 19mm | 22.2mm | 25.4mm | 28.6mm |
1 1/4" | 1 1/2" | 1 3/4" | 2" | 2 1/4" | 2 1/2" | 2 3/4" | 3" | 3 1/2" | 4" |
31.8mm | 38.1mm | 44.5mm | 50.8mm | 57.2mm | 63.5mm | 69.9mm | 76.2mm | 88.9mm | 101.6mm |
Alloy 317L (UNS S31703) is a molybdenum-bearing austenitic stainless steel with greatly increased resistance to chemical attack as compared to the conventional chromium-nickel austenitic stainless steels such as Alloy 304. In addition, Alloy 317L offers higher creep, stress-to-rupture, and tensile strength at elevated temperatures than conventional stainless steels. It is a low carbon or “L” grade which provides resistance to sensitization during welding and other thermal processes.
Specification Sheet Overview
for Alloy 317L (UNS S31703)
W. Nr. 1.4438:
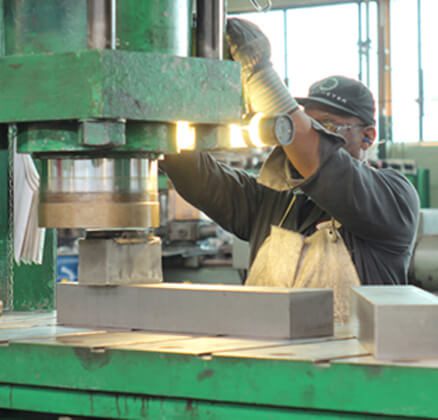
General Properties
Alloy 317L (UNS S31703) is a low carbon corrosion resistant austenitic chromium-nickel-molybdenum stainless steel. The high levels of these elements assure the alloy has superior chloride pitting and general corrosion resistance to the conventional 304/304L and 316/316L grades. The alloy provides improved resistance relative to 316L in strongly corrosive environments containing sulfurous media, chlorides, and other halides.
The low carbon content of Alloy 317L enables it to be welded without intergranular corrosion resulting from chromium carbide precipitation enabling it to be used in the as-welded condition. With the addition of nitrogen as a strengthening agent, the alloy can be dual certified as Alloy 317 (UNS S31700).
Alloy 317L is non-magnetic in the annealed condition. It cannot be hardened by heat treatment, however the material will harden due to cold working. Alloy 317L can be easily welded and processed by standard shop fabrication practices.
Corrosion Resistance
The higher molybdenum content of Alloy 317L assures superior general and localized corrosion resistance in most media when compared with 304/304L and 316/316L stainless steels. Environments that don’t attack 304/304L stainless steel will normally not corrode 317L. One exception, however, are strongly oxidizing acids such as nitric acid. Alloys that contain molybdenum generally do not perform as well in these environments.
Alloy 317L has excellent corrosion resistance to a wide range of chemicals. It resists attack in sulfuric acid, acidic chlorine and phosphoric acid. It is used in handling hot organic and fatty acids often present in food and pharmaceutical processing applications.
The corrosion resistance of 317 and 317L should be the same in any given environment. The one exception is where the alloy will be exposed to temperatures in the chromium carbide precipitation range of 800 – 1500°F (427 – 816°C). Because of its low carbon content, 317L is the preferred material in this service to guard against intergranular corrosion.
In general, austenitic stainless steels are subject to chloride stress corrosion cracking in halide service. Although 317L is somewhat more resistant to stress corrosion cracking than 304/304L stainless steels, because of its higher molybdenum content, it is still susceptible.
The higher chromium, molybdenum and nitrogen content of 317L enhance its ability to resist pitting and crevice corrosion in the presence of chlorides and other halides. The Pitting Resistance Equivalent including Nitrogen number (PREN) is a relative measure of pitting resistance. The following chart offers a comparison Alloy 317L and other austenitic stainless steels.
Cr | Mo | N | ||
304 Stainless Steel | 18.0 | — | 0.06 | 19.0 |
316 Stainless Steel | 16.5 | 2.1 | 0.05 | 24.2 |
317L Stainless Steel | 18.5 | 3.1 | 0.06 | 29.7 |
SSC-6MO | 20.5 | 6.2 | 0.22 | 44.5 |
1Pitting Resistance Equivalent, including Nitrogen, PREN = Cr + 3.3Mo + 16N
Chemical Analysis
Weight % (all values are maximum unless a range is otherwise indicated)
Nickel | 11.0 min.-15.0 max. | Sulfur | 0.030 |
Molybdenum | 3.0 min. - 4.0 max. | Silicon | 0.75 |
Carbon | 0.030 | Nitrogen | 0.10 |
Manganese | 2.00 | Iron | Balance |
Density
0.285 lbs/in3
7.89 g/cm3
Specific Heat
0.12 BTU/lb-°F (32 – 212°F)
502 J/kg-°K (0 – 100°C)
Modulus of Elasticity
29.0 x 106 psi
200 GPa
Thermal Conductivity 68°F (20°C)
8.1 BTU/(hr x ft x °F)
14 W/(m x K)
Melting Range
2540 – 2630°F
1390 – 1440°C
Electrical Resistivity
33.5 Microhm-in at 68°C
85.1 Microhm-cm at 20°C
Mean Coefficient of Thermal Expansion
°F | °C | in/in °F | cm/cm °C |
68-212 | 20-100 | 8.9 x 10-6 | 16.2 x 10-6 |
Mechanical Properties
Values at 68°F (20°C) (minimum values, unless specified)
0.2% Offset | Strength | in 2 in. | |||
---|---|---|---|---|---|
psi (min.) | (MPa) | psi (min.) | (MPa) | % (min.) | (max.) |
30,000 | 205 | 75,000 | 515 | 40 | 95 Rockwell B |
Fabrication Data
Alloy 317L can be easily welded and processed by standard shop fabrication practices.
Cold Forming
The alloy is quite ductile and forms easily. The addition of molybdenum and nitrogen implies more powerful processing equipment may be necessary when compared with the standard 304/304L grades.
Hot Forming
Working temperatures of 1652 – 2102°F (900 – 1150°C) are recommended for hot working processes. Do not work this alloy below 1742°F (950°C). If the final forming temperature falls below this threshold, a solution anneal of 1976 – 2156°F (1080 – 1180°C) is necessary. Rapid quenching is required.
Machining
The cold work hardening rate of Alloy 317L makes it less machinable than 410 stainless steel. The table below provides relevant machining data.
Operation | Tool | Lubrication | ||||||
---|---|---|---|---|---|---|---|---|
Depth-mm | Depth-in | Feed-mm/t | Feed-in/t | Speed-m/min | Speed-ft/min | |||
Turning | High Speed Steel | Cutting Oil | 6 | .23 | 0.5 | .019 | 11-16 | 36-52 |
Turning | High Speed Steel | Cutting Oil | 3 | .11 | 0.4 | .016 | 18-23 | 59-75 |
Turning | High Speed Steel | Cutting Oil | 1 | .04 | 0.2 | .008 | 25-30 | 82-98 |
Turning | Carbide | Dry or Cutting Oil | 6 | .23 | 0.5 | .019 | 70-80 | 230-262 |
Turning | Carbide | Dry or Cutting Oil | 3 | .11 | 0.4 | .016 | 85-95 | 279-313 |
Turning | Carbide | Dry or Cutting Oil | 1 | .04 | 0.2 | .008 | 100-110 | 328-361 |
Depth of cut-mm | Depth of cut-in | Feed-mm/t | Feed-in/t | Speed-m/min | Speed-ft/min | |||
Cutting | High Speed Steel | Cutting Oil | 1.5 | .06 | 0.03-0.05 | .0012-.0020 | 16-21 | 52-69 |
Cutting | High Speed Steel | Cutting Oil | 3 | .11 | 0.04-0.06 | .0016-.0024 | 17-22 | 56-72 |
Cutting | High Speed Steel | Cutting Oil | 6 | .23 | 0.05-0.07 | .0020-.0027 | 18-23 | 59-75 |
Drill ø mm | Drill ø in | Feed-mm/t | Feed-in/t | Speed-m/min | Speed-ft/min | |||
Drilling | High Speed Steel | Cutting Oil | 1.5 | .06 | 0.02-0.03 | .0007-.0012 | 10-14 | 33-46 |
Drilling | High Speed Steel | Cutting Oil | 3 | .11 | 0.05-0.06 | .0020-.0024 | 12-16 | 39-52 |
Drilling | High Speed Steel | Cutting Oil | 6 | .23 | 0.08-0.09 | .0031-.0035 | 12-16 | 39-52 |
Drilling | High Speed Steel | Cutting Oil | 12 | .48 | 0.09-0.10 | .0035-.0039 | 12-16 | 39-52 |
Feed-mm/t | Feed-in/t | Speed-m/min | Speed-ft/min | |||||
Milling Profiling | High Speed Steel | Cutting Oil | 0.05-0.10 | .002-.004 | 10-20 | 33-66 |
Welding
Alloy 317L can be readily welded by most standard processes. A post weld heat treatment is not necessary.